4Mを使った工場の品質管理法とトラブル対応術
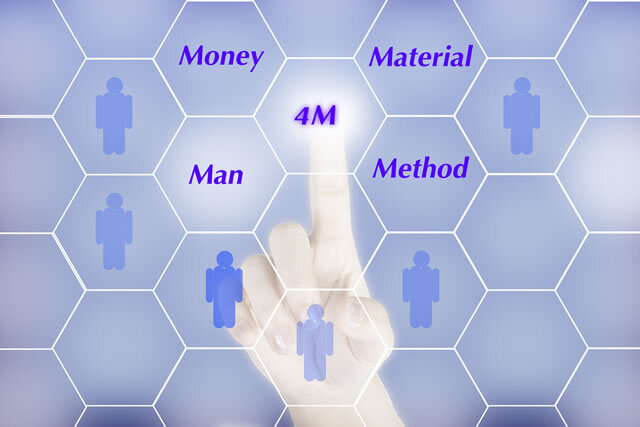
工場で不良品が発生した場合、担当社員のスキル不足や単純な機械トラブルとして片付けてはいないでしょうか。発生した問題を簡単に処理してしまえば、根本的な解決につながらず、今後も不良品が発生し続ける可能性もあります。
高品質な製品を顧客に届けるためには、適切な品質管理が重要になります。今回は4Mを用いた品質管理の方法について詳しくご説明します。
目次 [非表示]
1.生産現場の4Mとは
4Mとは、一般的に製造業で用いられる造語で、生産ラインを正常に動かし品質を管理するために必要とされる4つの要素を指します。品質管理の4Mは、以下の4つの単語の頭文字を取っています。
・Man:人間
・Machine:機械
・Method:方法
・Material:材料
上記の4Mを意識して日ごろの品質管理を行うことが、機械加工による生産の基本とされています。しかし、現在では「多品種少量生産」に移行した工場の時代背景を反映し、5M+1Eや6M といった概念も誕生しています。
5M+1E はMeasurement(検査・測定)とEnvironment(環境)を加え、6M でMeasurement(検査・測定)とManagement(マネジメント)を追加した概念ですが、今回は基本となる4Mに絞ってご紹介します。
2.4M視点で品質を管理する
品質管理では、4Mそれぞれの視点で維持管理を継続すると効果的であるとされています。その理由を詳しく見ていきましょう。
維持管理とは
守るべきルールを定め、日ごろから徹底することを維持管理と言います。
作業員の経験則や勘に沿った判断では毎日の作業や製品の品質に波ができてしまうため、ルールの作成と作業員への周知は、品質管理の第一歩となります。
4Mを活用した維持管理では、品質を保つために必要な規則をそれぞれ定め、確認しておく必要があります。
維持管理で必要なチェックポイント
4M視点で行う維持管理では、次のような項目を定めて実践していきます。
・Man:遅刻、欠勤、早退時の報告ルール、勤務シフト表、退職予定者の引継ぎ方法
・Method:正確な作業指示の伝達方法、作業する環境の設備条件の決定、作業順序などの作業マニュアル
・Material:伝票の書き方(材料の品名・品数など)、道具の整備や整理整頓方法、作業完了の報告ルール
・Machine:清掃・メンテナンスのルールと点検基準
上記は一例に過ぎません。各工場で品質管理に影響を及ぼすと考えられる項目を中心にルールを決定し、維持管理を行いましょう。
3.トラブル防止に不可欠な4Mの変化点管理
4Mに関する項目が変化することを変化点と捉え、変化点を事前に予測し、対応策をあらかじめ構築することを変化点管理と言います。
例えば、工場における変化点には、スタッフの退職や老朽化による機械の故障などが挙げられます。
変化点が発生すると、品質に影響するトラブルが起きやすいとされています。そのため、品質を一定に保つためには、トラブルの発生を前提とした変化点管理が欠かせません。
変化点には予測可能なものと不可能なものの2種類に分けられますが、対応策が異なってくるため、それぞれについて次章から詳しく見ていきましょう。
4.予測可能な変化点への対策
予測可能な変化点には、以下のような対策を行うと良いとされています。
事前にマニュアルを作成する
従業員の採用や退職による増減で担当作業が変わることは、予測可能な変化点のひとつです。特に離職により熟練作業員が減少すると、工場全体のスキルや作業スピードが落ち、生産に大きな影響を与える可能性があります。
この場合は、作業マニュアルの考案が効果的です。歴の浅い従業員でも理解できるマニュアルを事前に作成しておくと、品質のブレを軽減できます。
対応の優先順位をつける
変化点が与える品質への影響を考え、対応する優先順位を決めておきましょう。
生産ラインの機械を例に見ると、製造に使う機械の数は少なくないため、全て同じように管理することは簡単ではありません。そこで、生産への重要度を考えて機械をランク付けし、メンテナンスや管理の頻度を決めていきます。
そうすると経年劣化による故障や生産ラインの変動といった変化点にもスムーズに対応できます。
データを記録する
機械の動作数値や作業員の勤務時間、在庫の数といった日々のデータをきちんと記録することも大切です。
データの蓄積により、それぞれの正常値を把握でき、変化点に気付きやすくなります。変化点を早期に発見できれば、早く対策が打てるため損失を最小限に抑えられます。
ルールの周知を徹底する
作業方法やルールを変更する場合は、ルールの周知を徹底しましょう。
作業員は今までの方法が習慣づいているため、小さな変化でも作業に異常をきたし、ミスが発生する可能性があります。人的ミスを減らすために、作業員全員に対して必ずルールの共有を行いましょう。
5.予測できない変化点への対策
次に、予測できない変化点への対策について見てみましょう。あらかじめ予想できない変化点では、次のような対策が有効です。
報告ルールを定める
予測できない変化点が発生した場合、いかに早く対応するかがカギとなるため、トラブルに気づいた作業員が素早く管理者に伝達する仕組みがあると最適です。
予期せぬトラブルが発生したら「誰に」「何を」報告するのかを事前に明確化し、周知しておきましょう。
原因を究明し再発防止策をたてる
報告を受けた監督者はトラブルを4Mに分類し、どんな変化点がなぜトラブルに繋がったのか原因を究明していきます。
トラブルの原因究明には、蓄積していたデータを活用できます。異常値などから原因を究明して再発防止策を考え、新しくマニュアルを作成すると、今後は予測可能な変化点として管理が行えます。今後、同様のトラブルが発生しないような対応策を構築しておきましょう。
6.まとめ
製造業では、4M(人、機械、方法、材料)を用いた品質管理方法が基本とされています。4Mで行う維持管理の継続が重要ですが、時にはトラブルが発生する可能性も少なくありません。そのトラブルの元となる変化点を推測し、対策をたてる変化点管理も大切です。
変化点は予測可能な変化点と予測不可能な変化点に分けられますが、予測可能な変化点では誰でも対応できるようにマニュアルを作成する、予測不可能な変化点では報告ルールを決めるといったように、それぞれの対処法を明確にしておきましょう。