工場の安全対策とは?知っておくべき基本ポイント
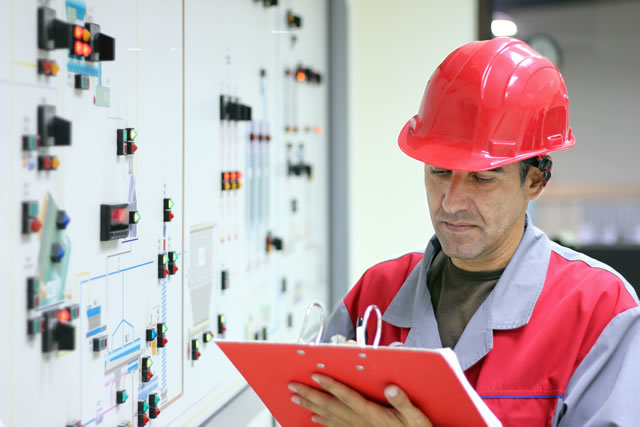
工場内では様々な機械が作動し、重量のあるものや化学物質をはじめとした、少し間違えば重大な事故を引き起こしかねないものが無数にあります。
そんな工場内において安全対策は必須であり、怠れば重大な事故を引き起こし、最悪の場合は命の危険もあります。
そこで今回は、工場の安全対策の基本についてご紹介していきます。
目次 [非表示]
1.工場のルールは危険を減らすためにある
工場には通常、安全を守るためのルールが設定されています。ルールによって工程が増え、作業効率に疑問を持つこともあるかもしれませんが、危険を避けるために作られた必要不可欠なものです。
大きな事故は、作業員の命や工場の存続にも関わります。どのような危険があるのかしっかり把握し、安全のためのルールを全作業員で徹底して守ることが求められます。
何か危険なことがあれば作業員同士でホウレンソウ(報告・連絡・相談)を行い、対策を立て、危機意識を共有することが大切です。
工場だけのデータではありませんが、厚生労働省によると、労働災害による死傷者数・死亡者数は減少傾向にあり、労働環境の安全性は改善されていると言えます。しかし、2016年でも年間928人が亡くなっています。
2.環境が作業員を守る~5S活動
5Sとは、工場などの製造業で、職場環境や安全性を改善するための考え方・スローガンです。以下の5つの要素から構成されます。
・整理(Seiri)
・整頓(Seiton)
・清掃(Seisou)
・清潔(Seiketsu)
・しつけ(Shitsuke)
・整理
必要なものと不要なものを明確に区分し、不要なものは処分しましょう。
工場では様々な物質を大量に扱います。使わないものを放置しておくと衛生面や作業環境などが悪化していきます。また、万が一の事故の際、放置していた物によって被害を拡大させる危険もあります。
・整頓
必要なものを誰でもすぐに取り出せるように、道具や資材の置き方・個数を決めて整頓しましょう。
作業の効率化はもちろん、紛失物の早期発見による混入事故の防止、危険な道具を扱う場合は安全性の向上にも繋がります。
・清掃
清掃は、ただゴミやホコリを取るだけではありません。
機械をスムーズに作動させるための定期的なメンテナンスに加え、環境や扱う物によっては、細菌や微生物の除去、昆虫発生の防止などに気を使う必要もあります。
・清潔
これまで解説してきた「整理」「整頓」「清掃」の3Sを維持することを指します。
「清潔」を保つためには、すべての作業員が整理・整頓・清掃を無理なく遵守できるような環境整備やルール化が必要です。
・しつけ
清潔を保つためのルール作りと、それを守る習慣を身に付けることが「しつけ」です。
「しつけ」は、叱って強制的に動かすという意味ではなく、習慣づけのための訓練です。全従業員が5Sやルールを徹底することで、事故が起こりにくい環境が生まれます。
3.危険は訓練で予知できる~KYT
「KYT」とは危険(Kiken)予知(Yochi)訓練(Training) の頭文字を取った造語で、危険に対する感受性や集中力、問題解決能力を高めるために行う訓練のことです。
KYTには「基礎4ラウンド法」と呼ばれる訓練手法があり、事故が発生しそうな状況のイラストを見ながら行うパターンと、実際の現場を見ながら行うパターンなどがあります。
手順は以下のとおりです。
1R(ラウンド):潜んでいる危険をあぶりだす
2R(ラウンド):重要度を分類する
3R(ラウンド):重度の高い項目の対策案を出し合う
4R(ラウンド):チーム共通のルールとする
1R:潜んでいる危険をあぶりだす
5名前後(活発に意見を言い合える人数)でイラストや現場を見て、考えられる危険を挙げていきます。ポイントは、どんな意見も否定せずに、思いつく限りの問題を洗い出すことです。
挙げられた危険は、ホワイトボードなどに書き、一覧にします。
2R:重要度を分類する
1Rで挙がった考えられる危険の中から、重要だと思われる項目に◯をつけます。〇の中から、再び重要なものを絞り込み、◎をつけて「危険ポイント」とします。
例えば、各々が重要だと思う項目をメモに書き、2名以上が重要とした項目を○、3名以上が重要とした項目を◎などとしても良いかもしれません。
〇がない項目、◯がついた項目、◎がついた項目と、重要度を三段階に分け、特に重要と判断した◎の「危険ポイント」を全員で指差しながら唱和します。
3R:重要度が高い項目の対策案を出し合う
2Rで挙げられた「危険ポイント」を解決する対策法について、意見を出し合います。出た対策法も一覧にしましょう。
4R:チーム共通のルールとする
3Rで挙げられた対策法の中から、実施する項目を決定しマークをつけて、「チーム共通ルール」にします。
共通ルールは、掲示板等に貼り出すと効果的です。 最後に「危険ポイント」と「チーム行動目標」を指差し唱和で確認しましょう。
4.記録と報告は将来の事故を防ぐ~ホウレンソウとヒヤリハット
「ホウレンソウ」とは、「報告・連絡・相談」の略称であり、「ヒヤリハット」とは、工場などの作業場で事故には至らなかったものの「ヒヤリとした」「ハッとした」体験のことを言います。
アメリカのハーバート・ウィリアム・ハインリッヒが、数千件の労働災害を調査し、「1件の重大な事故には、29件の軽い事故と300件のヒヤリハットがある」という法則を1931年にIndustrial Accident Prevention-A Scientific Approachという著書で発表しました。
この法則は「ハインリッヒの法則」や「1:29:300の法則」とも呼ばれ、現代でも労働災害を防ぐための考え方として有名です。
この法則を元に考えると、事故を防ぐためには、軽い事故やヒヤリハットもできるだけ防がなければなりません。ヒヤリハットを記録するノートなどを作っておきましょう。
ヒヤリハットを体験したら欠かさず記録し、全体ミーティングなどで報告します。
改善が必要な場合は管理者に相談し、具体的な対策を考えましょう。ヒヤリハットの事例を記録し、全員で共有することが重大な事故の防止に繋がります。
5.まとめ
労働災害は年々減少傾向にありますが、2016年でも年間928人が亡くなっています。様々な危険物を扱う工場では1つの事故が命に関わることもあり、安全を守るためにルールの厳守を徹底しなければなりません。
具体的な安全対策として5S(整理・整頓・清掃・清潔・しつけ)を全員で徹底しましょう。他にも、KYT(危険予知訓練)の4R法実施、ヒヤリハットの記録など、安全対策にむけた意識改革や環境づくりが大切です。
安全対策を「行いすぎる」ということはありません。作業員全員が安心して働ける工場にするために、日々実践していきましょう。